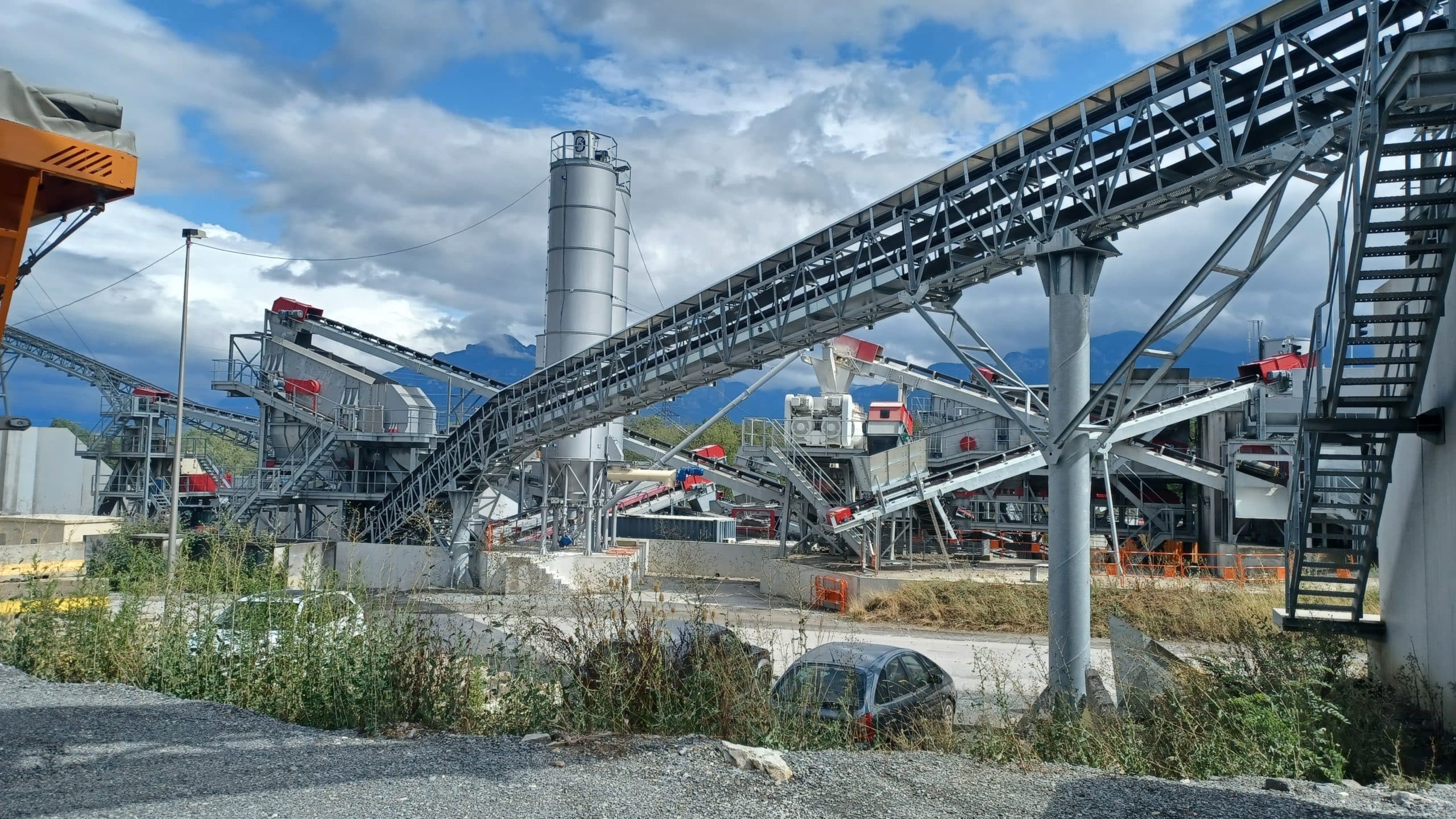
ERMAC: Innovation and Tailor-Made Solutions Serving Industry
Published on 17 July 2025
In the field of bulk material processing, ERMAC stands out for its ability to design and integrate custom-built installations, an approach grounded in unique expertise and a strong reputation for innovation. As a key player in the materials processing sector, ERMAC’s engineering know-how allows it to tackle complex technical challenges, as demonstrated by their IPAQ project. We spoke with site manager Bruno Bordoni and technical sales engineer Anthony Darcon.
Over 50 Years in Quarrying and Recycling
Can you briefly introduce ERMAC?
Bruno Bordoni: ERMAC was founded in 1969 to design and integrate systems for material processing. Our core business is to design, manufacture, assemble, and commission industrial equipment for quarries, sand pits, and waste recycling facilities, handling materials such as wood, glass, or bottom ash. We are at the same time an engineering office, manufacturer, and integrator.
Where can we find your machines?
Anthony Darcon: Our machines are used in many limestone, basalt, porphyry, and granite quarries. Extracted rock is processed through our systems to produce standardized aggregates. They’re also found in recycling centers where they help process and recover various materials.
What sets ERMAC apart from the competition?
B.B.: We offer tailor-made solutions. We adapt to the specific needs of our clients with custom systems. We also provide a range of standard products, such as belt conveyors. Our added value lies in optimizing installations to reduce operating costs.
How do you collaborate with other Rouby Group companies?
ERMAC integrates products from other group companies like Chauvin or SINEX Industrie into its systems, enabling us to deliver even more complete solutions.
What is the geographic scope of your business?
Although we have strong roots in the Auvergne-Rhône-Alpes region, we operate nationwide. International expansion is on the table, but our priority is to consolidate growth in France.
IPAQ: An Engineering Challenge for Glass Recycling
What made the IPAQ project a technical challenge?
A.D.: IPAQ is a glass recycling facility run by Maltha Glass, a Dutch group, located near Izon in the Gironde region. After collaborating on a previous facility, they approached us for this new processing line.
What was the main challenge of the project?
The biggest challenge was space: the new installation had to fit within an existing building already 80–90% full. We had to fit four machines and their conveyors within a 5 square meters space, across multiple levels.
How did you meet that challenge?
Through close collaboration with the client, we did optimize every square meter. Our strength lies in designing compact, efficient layouts with fewer scrapers, rollers, and belts, leading to lower maintenance and cost savings for the client.
What was the project timeline?
B.B.: After approval, the project took a year to complete: 3 months of design, 6 months of manufacturing, and 3 months for assembly and commissioning. Success came from good planning and early collaboration with the client.
What about the environmental impact?
A.D.: We recommend energy-efficient machines, low-power motors, and systems that reduce noise and dust. Environmental responsibility is becoming central to our work, it’s an ongoing effort.
Is ERMAC moving more toward recycling activities?
B.B.: Yes, because the aggregates industry is evolving: 75% of aggregates still come from quarries, but recycling is growing. We’re seeing changes in how incineration residues and construction waste are managed. We’re adapting to this transition with suitable solutions.